Taiyang has been committed to providing the corrugated cardboard packaging market with complete plant scrap handling solutions, aiming at solving the problem of waste paper recycling, transporting and baling in the corrugated packaging industry. With reasonable combination of various equipment and accurate data analysis, our scrap handling solution ultimately realizes an automated and unmanned scrap handling process of collection, transporting, compression and baling of wastes produced during corrugated cardboard production, printing, die-cutting and other processing operations. This waste handling system significantly enhances the working efficiency of scrap handling, reduces the costs of labor, warehousing and transportation. Besides, the air quality of the working environment can be greatly improved.
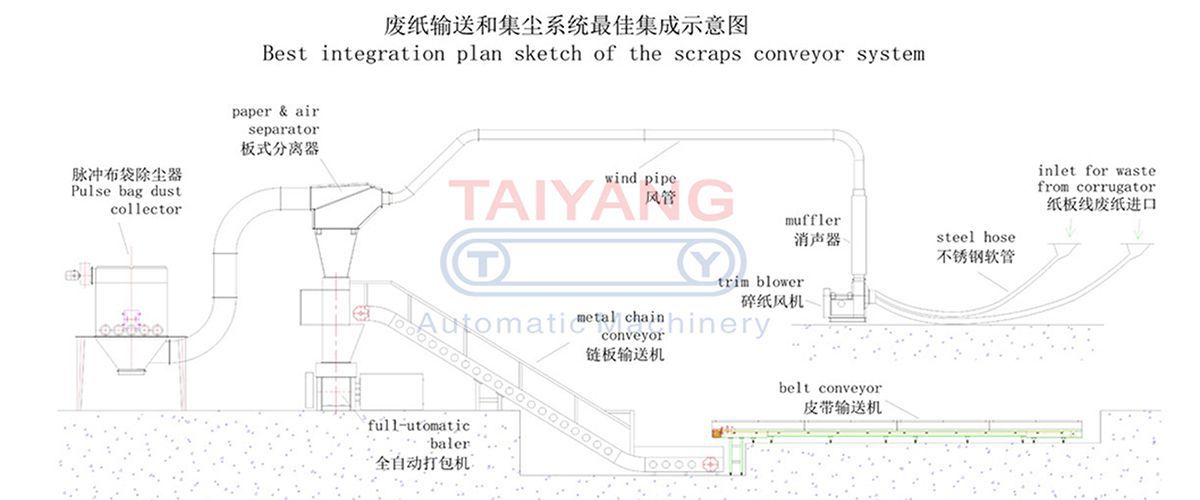
Optimal integrated solution for waste handling in corrugated board industry
- Waste paper from corrugating line and printing press should be aggregated for packaging;
- Usage of trim blower during waste paper conveying should be kept minimum, so that to reduce energy waste, and noise and dust pollutions.
Principles of the optimal solution
- The place for waste cardboard collection should be set as close as possible to the baling press;
- Keep the usage of trim blower minimum;
- Paper dust from printing press can be collected and handled with air separator.
Components of waste handling system include
Belt conveyor, trim blower, industrial shredder for cardboard and paper, automatic baling press, air separator, pulse jet baghouse dust collector.
Belt conveyor plays an essential role in paper waste collecting and handling. It collects and conveys the scrap from the printing machine and die-cutting machine directly to the baling room for further processing. If the path for scrap clearance is long or contains many curves, trim blower could be connected to convey the scrap to baling room through pipeline. Our waste paper belt conveyor is featured by compact structure, less floor space, high energy efficiency and low noise level, offering stable and reliable operation with the ability to integrate into an automatic scrap handling system.
View More Functions of trim blower include cutting waste paper into scrap, and providing transport power to convey scrap to the baling room through pipeline for further processing. It is usually equipped with a muffler and an air separator, so as to reduce noise and dust pollutions.
Features: high energy consumption, high noise and dust pollutions. (so that its usage should be minimized!)
With the shredder, corrugated cardboard whether flat or tubed can get crushed and shredded into scarp for further processes of the automatic baling press.
Features- Blades/teeth on the cutting shaft are made of special alloy steel with special technical processes, featuring high strength and good wear resistance;
- Low rotational speed of the cutting shaft, low energy consumption and noise pollution;
- Promotes quantity and total value of the recycled waste paper;
- Highly-automatic, labor-saving;
- Able for crushing and cutting both flat cardboard and cardboard tube.
The baling press is used to perform baling and recycling on waste paper, cardboards, etc. in a fully-automatic manner. This baling machine mainly consists of bale chamber, main hydraulic cylinder, energy saving hydraulic system, hopper, hydraulic cylinder for compressing bale, MITSUBISHI PLC control system, automatic tying mechanism, etc. Newly designed oil circuit allows for high working efficiency with low consumption. Automatic tying system wraps tie steel wires around the bale after the bale is completely compacted, which prevents it from becoming loose.
View MoreTo separate air and waste paper dust from their high-pressure mixture, two types of air separators can be employed: rotary material separator, and cyclone separator. Inlet of the air separator is usually attached to trim blower’s outlet. Normally, exhausted air from the rotary material separator still contains large quantity of paper dust, and is therefore required to be filtered by pulse jet baghouse dust collector before discharge, and filtered air particulate matter can reach PM2.0 level. Exhausted air from cyclone separator contains little paper dust than that of separator with pulse jet filter, so if the emission standard isn’t too strict, the air from the cyclone separator could be discharged directly.
View MoreTo remove paper dust from the internal filter media surface with bursts of compressed air, so that outlet air from inertial separator can get cleaned. Main box of the collector is divided vertically into three sections: lower section, middle section, upper section, and a dust hopper is attached at the bottom of the main box. During the cleansing process, dirty air horizontally enters the hopper, where heavy coarse dust falls down directly into. Lighter dust then goes up with the air through the lower and middle section, dust gets drawn against the outer surface of the filter bags, retained and stored, while the cleaned air pass the upper section and get discharged. The pulse jet baghouse dust collector can equip PLC for automated operation of valves to control air outlet, pulse air input and dust discharge automatically.
View MoreNote: Maximum pressure of the waste handling system is guaranteed, but some configurations and technical parameters might be adjusted for improvements, and the minor adjustments will go without prior notices.
We offer advanced and cost-effective intralogistics equipment as well as professional intralogistics solutions for corrugated board industry. Tell us your strategic objectives and requirements, and we can offer you planning and technical support services:
- If you are about to construct a new plant, we can help with designing the facility, and offer process planning and intralogistics system planning;
- If you have already constructed a plant, but is not ready to run yet, we can offer process planning and intralogistics system planning services;
- If you are currently running the factory, and you want to optimize your production, we can offer consultations and examinations on rationality of your process planning, and design an optimal process re-planning if needed.
Except some special occasions, most of our products are non-standard and customizable. Units and modules to consist our intralogistics system with the same or similar functions may be in different specifications, but their basic structures and mechanisms are the same.
To customize intralogistics system or devices, we’ll discuss first to make sure of the intralogistics planning, with which the specifications and configurations of all units are determined, and the devices we offer are customized according to the specification determined in the plan. Note that control system is customized according to the requirements of the plan as well.
Since many components of our products are non-standard, per-determining the lead time is difficult. Order quantity and device complexity can both influence the delivery date.
Deposit takes 40% of the total price, and 60% should be paid before delivery; payment can be finished via TT, LC, etc.
Taiyang has abundant well-experienced aftersales personnel and spare part storage in China, so that we can respond to requests very quickly.
- Response to issues: 7×24 response; online guidance and problem-shooting will be offered within 24 hours after malfunctions occur;
- 1-year free warranty;
- Lifetime paid service: we offer paid services and spare parts for the most favorable prices to make sure our devices operate reliably and safely within their lifespans.